3D Printing saddle advantages and disadvantages
Summary of Advantages and Disadvantages of 3D Printing Saddles
Advantages
1. Customized support and comfort
Through 3D printing technology, honeycomb structures can be accurately designed to adjust softness and hardness in different areas, such as strengthening support in the ischium area and reducing pressure in the perineum, achieving a "soft where soft, hard where hard" effect, significantly improving riding comfort.
Adopting ergonomic design, it conforms to the curve of the buttocks, reduces friction and sliding during cycling, and lowers the risk of soft tissue compression.
2. Breathability and lightweight
The honeycomb hollow structure is naturally breathable, smaller in size, and easy to clean, improving the stuffiness of traditional seat cushions.
Some brands, such as Pantani, have achieved lighter weight than traditional seat cushions by optimizing materials and structural design.
3. Material durability
3D printed liquid polymers or high elasticity materials (such as EM materials from Qingfeng Technology) are not prone to collapse and have better resilience than traditional foam materials after long-term use.
4. Production flexibility
Fast production without the need for mold opening, supporting personalized customization and rapid iteration, reducing inventory pressure.
Disadvantages
1. High cost
The initial investment and material cost of 3D printing technology are relatively high, resulting in product prices generally higher than traditional seat cushions..
Difficulty in cleaning and maintenance.
The gaps in the honeycomb structure are prone to accumulate dust and sediment, and are difficult to thoroughly clean. Long term use may affect its appearance.
2. Insufficient adaptability of some products
There are significant differences in the design of different brands (such as the difference in the curling degree of the Lightning Power Mirror compared to traditional models), and it is necessary to adjust the seat height or riding posture to adapt.
Low end products may have materials that are too hard or support designs that are not perfect, requiring self adjustment of position to avoid friction.
3. Weight and material limitations
Some high-end models are heavier than traditional carbon fiber seat cushions due to the use of more materials or titanium rail designs.
At present, the types of materials available for 3D printing are limited, and some high-performance materials have not yet become popular.
Purchase suggestions
Priority seating test: Due to significant individual differences, it is recommended to measure the width of the ischium and test ride to avoid affecting the experience due to compatibility issues.
Pay attention to brand technology: Brands such as Lightning and Qingfeng Technology have mature technology in the field of 3D printed seat cushions, but need to balance price and performance.
Applicable scenarios: It is more recommended to pursue long-distance comfortable riding or professional training scenarios, and traditional products with higher cost-effectiveness can be considered for short distance commuting.
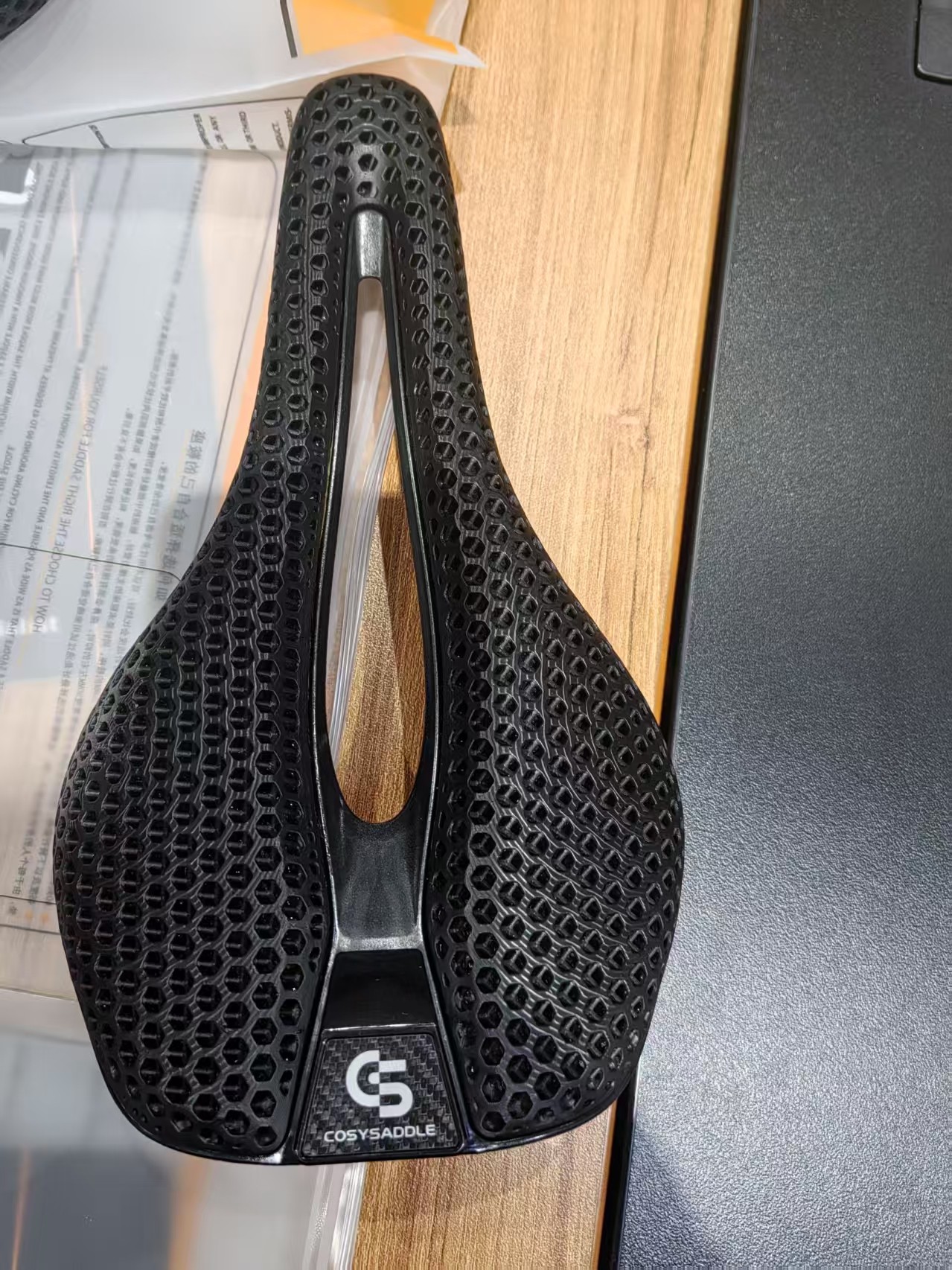
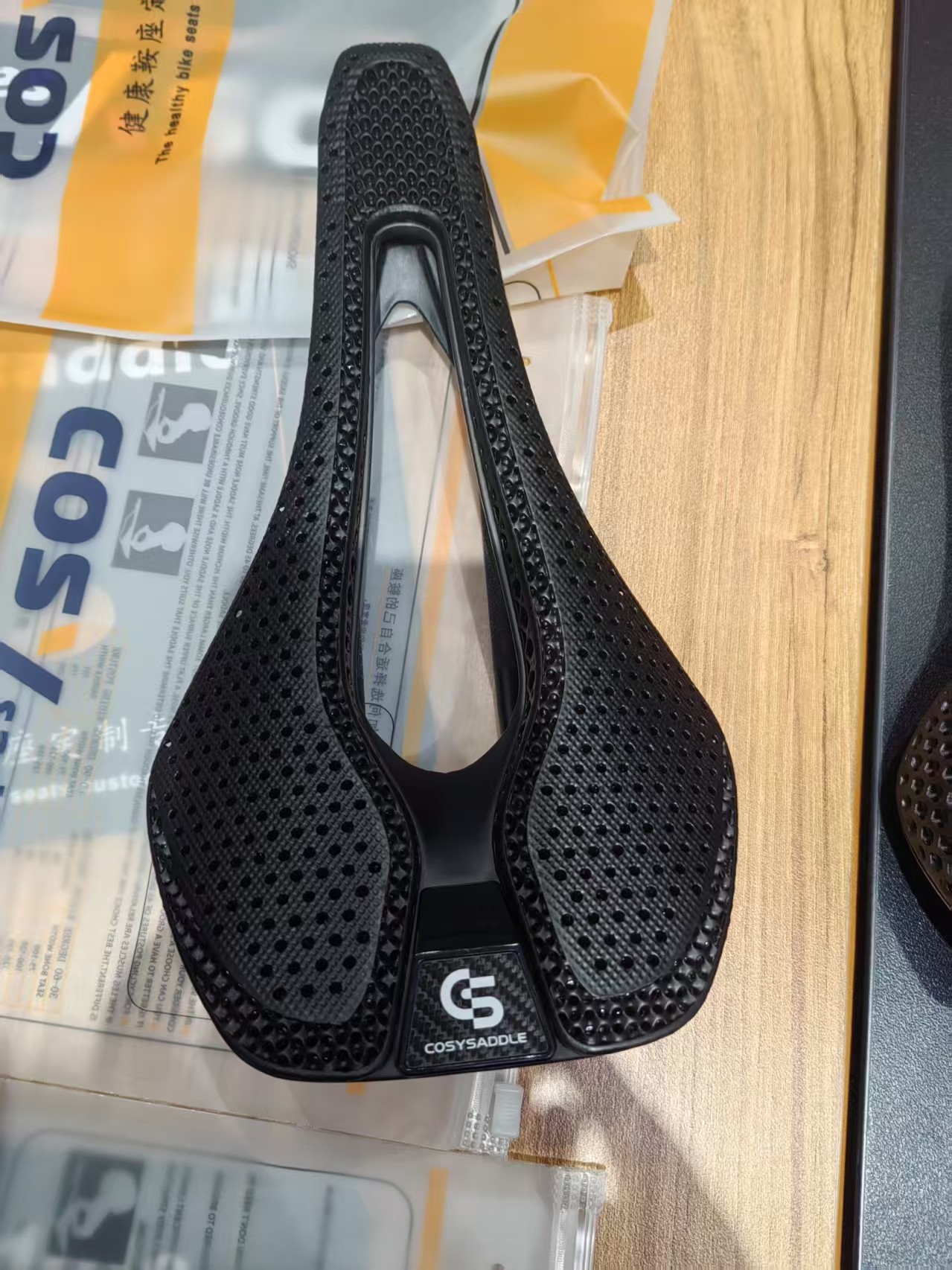
