The emergence of 3D printed seat cushions has solved this defect.
The bicycle seat cushion is one of the important components for the intimate contact between the rider and the bicycle, usually made of foam material. However, the resilience of foam materials will weaken over time (seat cushion collapse). For long-distance riders, long-term contact with the seat cushion can easily cause nerve pain, numbness, and urinary problems, seriously affecting the riding experience. The emergence of 3D printed seat cushions has solved this defect.
1. Traditional saddle material: PU, TPU foam material, silicone; 3D printing saddle material: high-performance elastic material EM
2. Traditional saddle lifespan: irreversible deformation may occur after prolonged use; 3D printed saddle lifespan: After 1 million bending tests, the resilience remains the same as before
3. Traditional saddle design: solid material filling, hollow openings, and possible pressure points at the edges; 3D printing saddle design: lattice structure, variable density in different areas, good shock absorption, strong support
4. Traditional saddle performance: The support force is not fixed and is usually soft/hard; 3D printed saddle performance: Different functional zones have different softness and hardness, with smooth changes, effectively reducing sciatic pressure
5. Traditional saddle breathability: The surface material is closed, resulting in poor breathability; 3D printed saddle breathability: hollow lattice structure, strong breathability
6. Traditional saddle manufacturing process: injection molding, filling, skinning, and adhesive bonding; 3D printing saddle manufacturing process: integrated molding
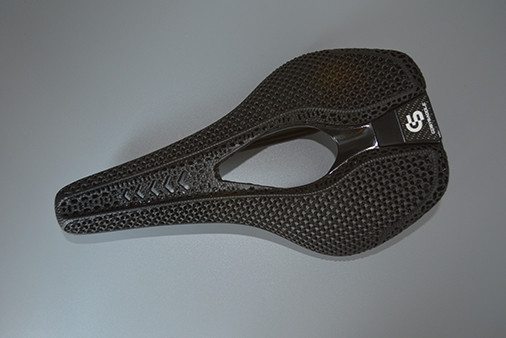
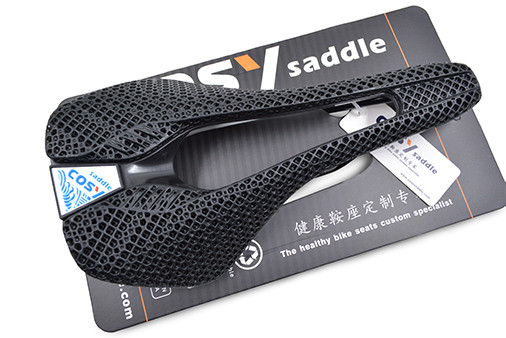
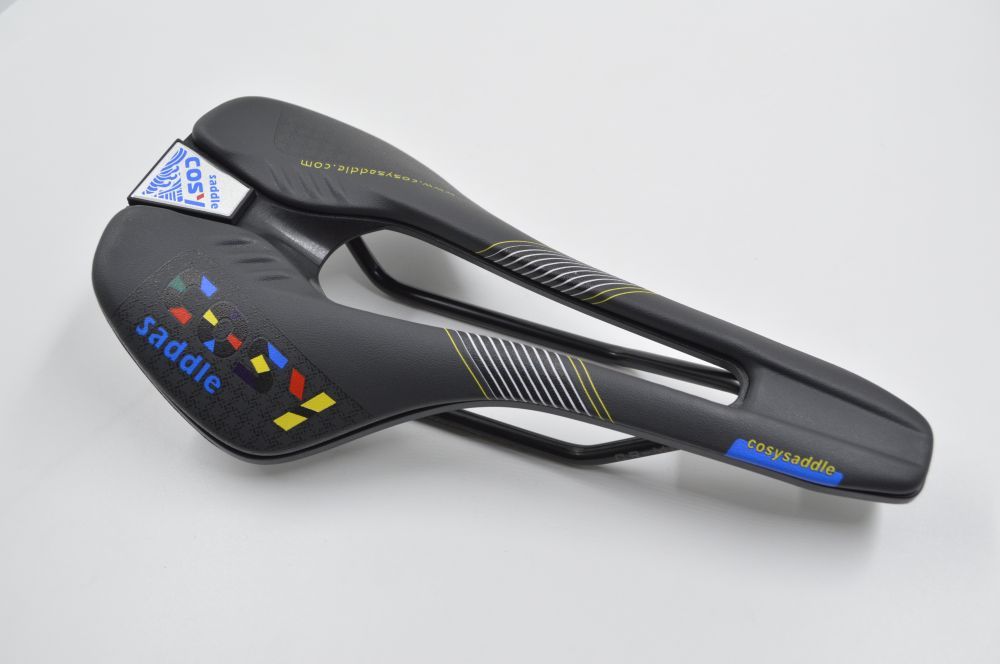
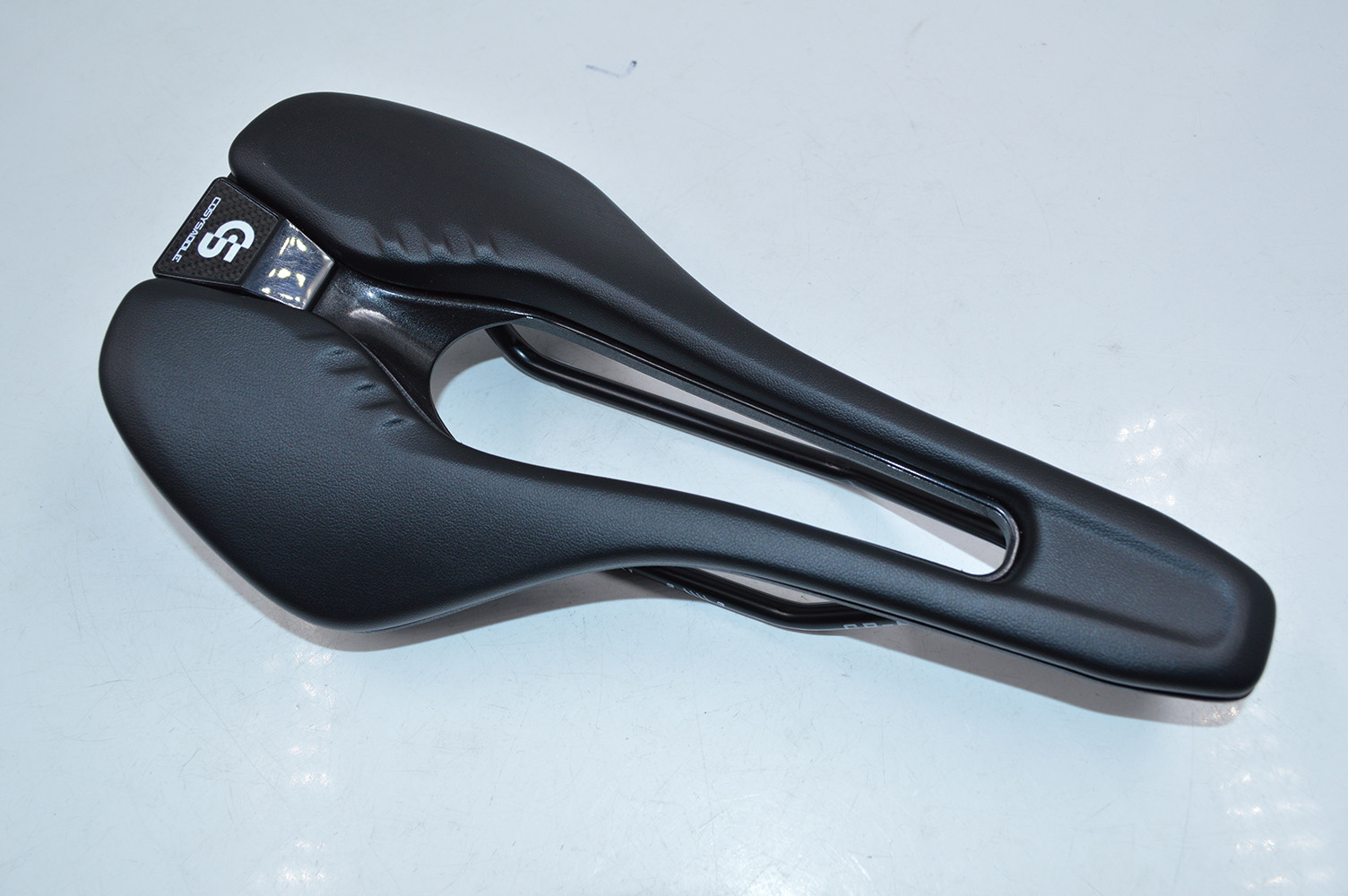