Comparison between 3D print bicycle saddle and traditional bicycle saddle
3D printed saddle:
Material: high performance elastic material EM
Lifespan: The resilience remains the same after 1 million bending tests
Design: lattice structure, variable density in different areas, good shock absorption and strong support
Performance: Functional partitions are different in softness and hardness, and the changes are gentle, effectively reducing ischial pressure.
Breathability: Hollow lattice structure, strong breathability
Production process: one-piece molding
Traditional saddle:
Material: PU, TPU foam material, silicone
Lifespan: Irreversible deformation will occur after long-term use
Design: Solid material filled, hollow openings, edges may create pressure points
Performance: The support force is not fixed, usually soft or hard
Breathability: The surface material is closed and the air permeability is poor
Production process: injection filling molding, glue pasting
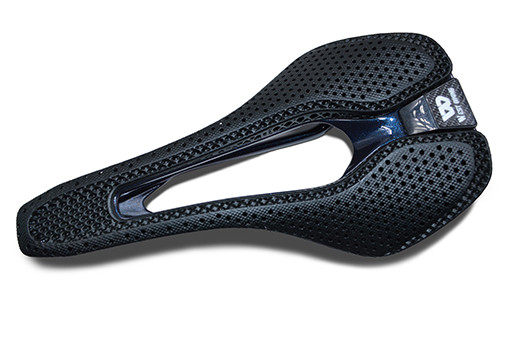
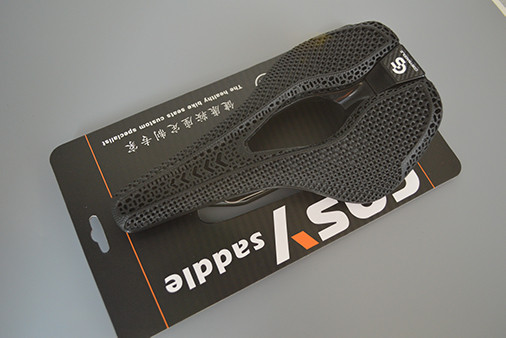
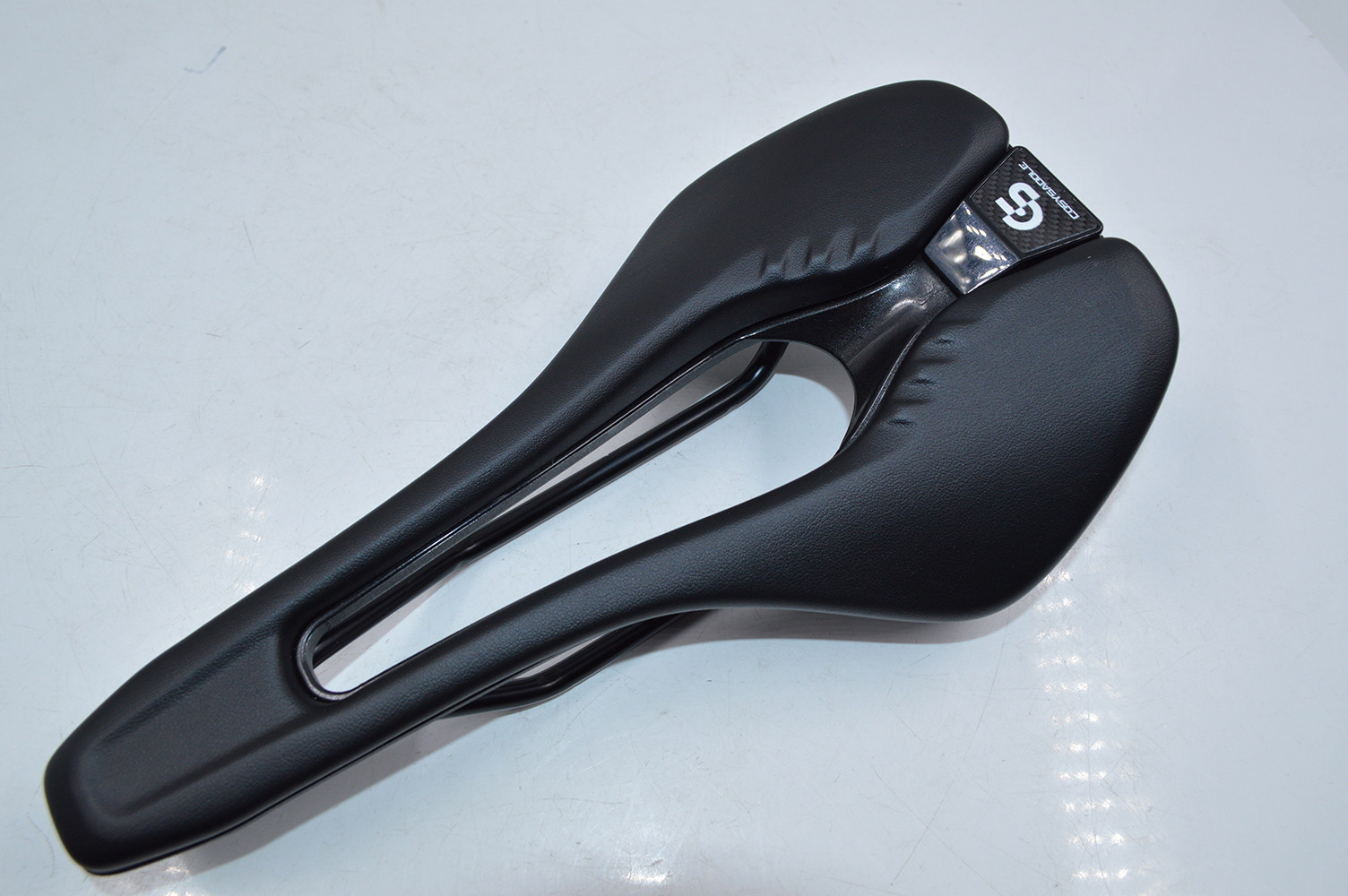
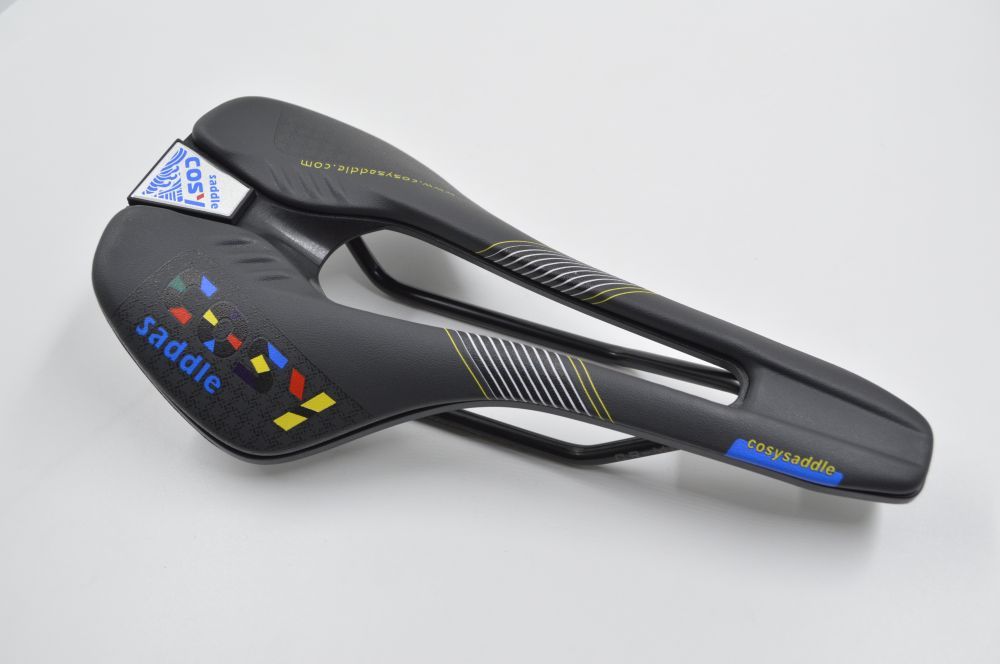